デジタルトランスフォーメーション(DX)は、現代の製造業における競争力強化と効率改善のために不可欠な要素となっており、その中でも特にCADデータの品質は極めて重要な要素として注目されています。CADデータは、設計から製造に至るまでの全プロセスにおいて中心的な役割を果たし、データの精度と一貫性が製品の品質を左右します。そのため、製造業では高品質なCADデータを維持しつつ、効率的なデータ処理と管理が求められています。
DXの進展に伴い、製造業は従来の業務プロセスを見直し、デジタル技術を駆使して業務全体を再構築しています。この過程では、CADデータの品質管理が特に重視され、製品の設計段階でデータの正確性を確保することが、後の製造プロセスにおけるトラブルを回避するための鍵となります。CADデータの不整合やエラーが発生すると、製造工程での不具合やコストの増大、納期の遅延につながる可能性が高く、そのためにはCADデータの品質検証が重要な役割を果たします。
製造業におけるDXの取り組みの一環として、CADデータの品質管理は単なるデータの確認作業にとどまらず、全社的な品質保証プロセスの一部として位置付けられています。特に複雑な製品設計においては、各設計データの精度が製品の性能に直結するため、厳密なデータ検証が必要とされます。このような背景から、多くの企業はCADデータの品質を維持するために、自動化された検証ツールや高度なデータ解析技術を導入しています。
たとえば、バイナリー解析を用いたツールを活用することで、異なるフォーマット間でのデータ変換や統合を容易にし、複数の設計システムで作成されたデータ間の不整合を迅速に検出することが可能になります。これにより、設計段階でのミスを早期に発見し、修正することができ、最終的な製品の品質を向上させるとともに、コスト削減と開発期間の短縮が図られます。
さらに、CADデータの品質管理には、データの保存や長期的な利用を考慮した管理も含まれます。製品ライフサイクルが長い産業では、設計データの長期保存が求められるため、適切なデータフォーマットと保存方法を選択することが重要です。これにより、将来的なデータの再利用が可能となり、開発コストをさらに削減することができます。
総じて、DXの成功にはCADデータの品質管理が不可欠であり、そのためには高度な技術とツールの活用が求められます。高品質なCADデータを基盤にすることで、製品設計の精度と一貫性が保たれ、製造プロセス全体の効率が向上します。このような取り組みは、競争が激化するグローバル市場において、製造業が持続可能な成長を遂げるための重要な要素となっています。今後も、DXの進展とともにCADデータの品質管理の重要性はますます高まり、製造業全体の発展に大きく貢献することでしょう。
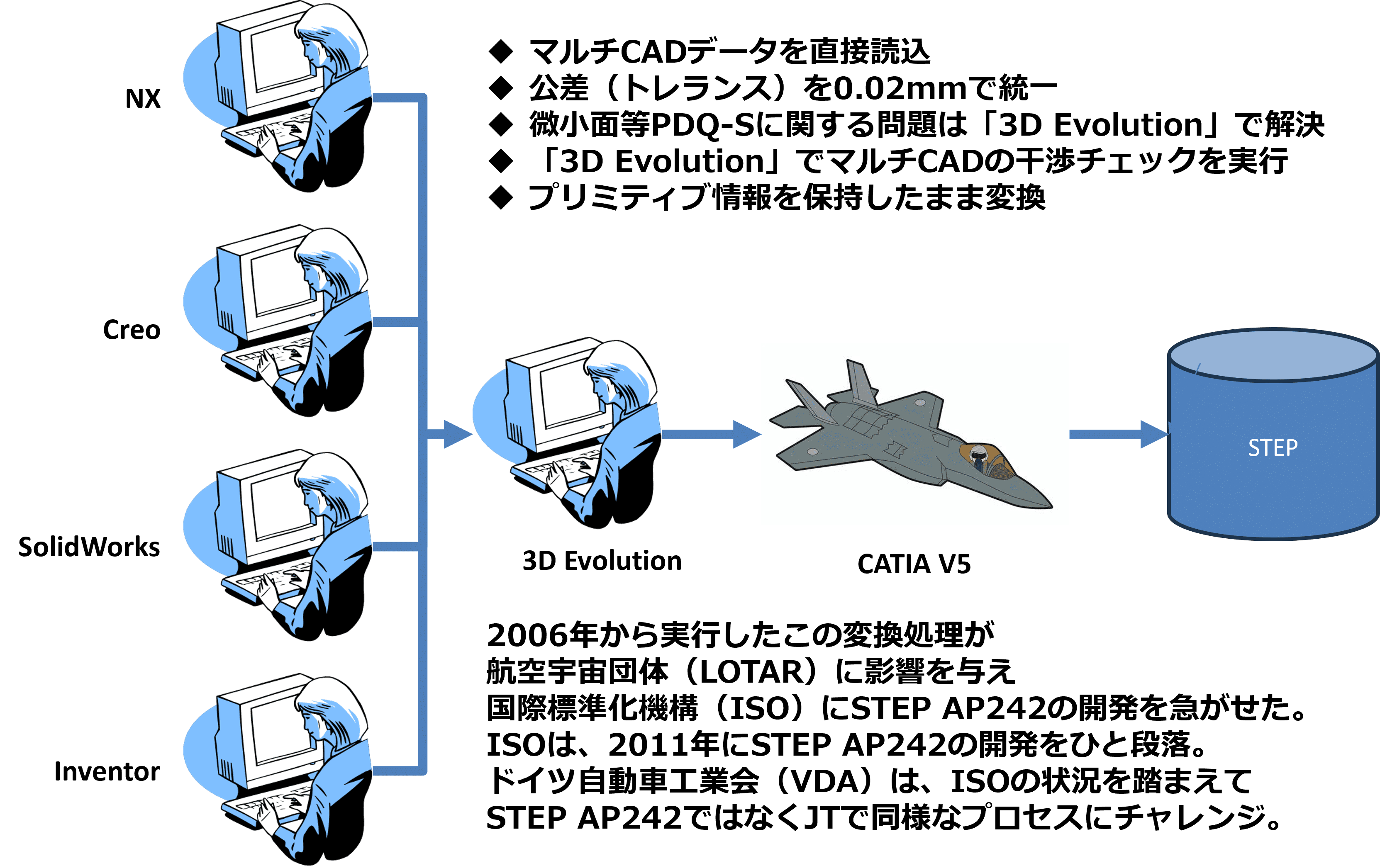